Fasteners and Machining: Trick to Reliable and Trusted Manufacturing
Fasteners and Machining: Trick to Reliable and Trusted Manufacturing
Blog Article
Navigating the Globe of Fasteners and Machining: Strategies for Precision and Rate
In the intricate world of bolts and machining, the quest for precision and rate is a continuous difficulty that requires meticulous interest to information and critical planning. From comprehending the varied range of bolt kinds to selecting ideal products that can withstand extensive needs, each step in the process plays an essential duty in accomplishing the wanted outcome. Precision machining strategies further raise the intricacy of this craft, needing a fragile equilibrium between technological expertise and ingenious strategies. As we explore the approaches that can improve both speed and performance in this domain, the interplay in between quality assurance procedures and functional excellence emerges as a critical centerpiece.
Understanding Fastener Types
When selecting fasteners for a task, recognizing the different types available is essential for guaranteeing optimal efficiency and dependability. Fasteners are available in a broad range of kinds, each created for certain applications and needs. Bolts are used with nuts to hold materials together, while screws are flexible bolts that can be utilized with or without a nut, depending upon the application. Nuts, on the other hand, are inside threaded fasteners that friend with screws or screws, providing a secure hold. Washing machines are crucial for dispersing the load of the bolt and stopping damage to the product being secured. Furthermore, rivets are permanent bolts that are suitable for applications where disassembly is not needed. Comprehending the distinctions in between these fastener kinds is necessary for selecting the right one for the job, making sure that the connection is solid, resilient, and reliable. By picking the suitable bolt type, you can optimize the efficiency and long life of your project - Fasteners and Machining.
Picking the Right Materials
Recognizing the significance of picking the appropriate materials is critical in making sure the optimum performance and reliability of the selected bolt types talked about formerly. When it involves bolts and machining applications, the material choice plays a critical role in identifying the general toughness, resilience, rust resistance, and compatibility with the desired atmosphere. Different products supply differing residential or commercial properties that can substantially impact the efficiency of the fasteners.
Usual materials utilized for fasteners consist of steel, stainless-steel, brass, titanium, and light weight aluminum, each having its distinct toughness and weaknesses. Steel is renowned for its high toughness and sturdiness, making it appropriate for a variety of applications. Stainless-steel offers outstanding rust resistance, suitable for atmospheres prone to moisture and chemicals. Light weight aluminum is light-weight and corrosion-resistant, making it suitable for applications where weight decrease is critical. Brass is usually selected for its aesthetic appeal and superb conductivity. Titanium is understood for its outstanding strength-to-weight ratio, making it suitable for high-performance applications. Choosing the right product includes considering variables such as stamina requirements, ecological conditions, and spending plan restrictions to ensure the wanted performance and long life of the fasteners.
Precision Machining Techniques
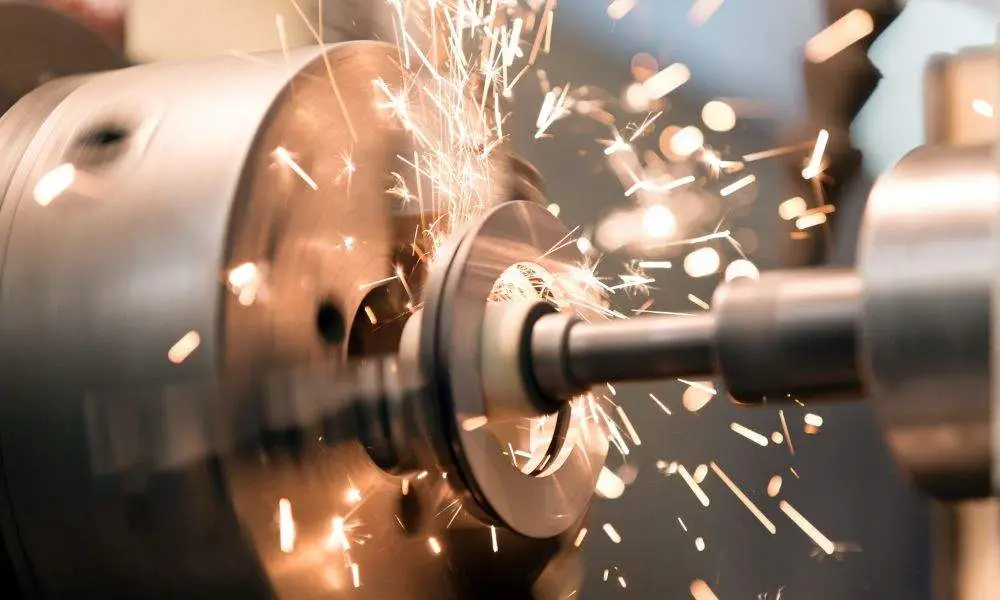
Along with CNC machining, various other precision methods like grinding, turning, milling, and boring play essential roles in bolt manufacturing. Grinding helps accomplish great surface finishes and limited dimensional resistances, while turning is commonly made use of to create round components with exact diameters. Milling and exploration procedures are necessary for shaping and producing openings in bolts, guaranteeing they satisfy exact specs and feature properly.
Enhancing Rate and Efficiency
To enhance fastener manufacturing procedures, it is vital to simplify operations and execute effective approaches that complement precision machining techniques. One key method for boosting rate and performance is the implementation of lean manufacturing principles. By reducing waste and concentrating on constant enhancement, lean techniques aid maximize and remove traffic jams operations. In addition, spending in automation modern technologies can substantially improve production speed. Automated systems can deal with repetitive tasks with accuracy and rate, permitting employees to concentrate on more complicated and value-added activities. Adopting Just-In-Time (JIT) supply monitoring can likewise enhance efficiency by guaranteeing that the best materials are available at the correct time, minimizing excess supply and minimizing lead times. Fostering a society of cooperation and communication amongst team members click for more info can boost overall performance by advertising transparency, analytic, and development. By incorporating these methods, producers can attain a balance in between speed and accuracy, eventually boosting their one-upmanship in the fastener market.
Quality Assurance Procedures
Executing extensive top quality control procedures is vital in making sure the reliability and uniformity of fastener products in the production process. Fasteners and Machining. Quality control actions include different stages, beginning from the choice of raw products to the final inspection of the ended up fasteners. This entails examining factors such as product toughness, composition, and stamina to ensure that the bolts meet market criteria.
Regular calibration of tools and machinery is important to keep uniformity in production and make sure that bolts meet the necessary resistances. Implementing rigorous protocols for determining and resolving problems or non-conformities is crucial in protecting against substandard products from going into the marketplace. By developing a comprehensive top quality control structure, manufacturers can support the track record of their brand name and deliver fasteners that meet the highest requirements of performance and longevity.
Final Thought
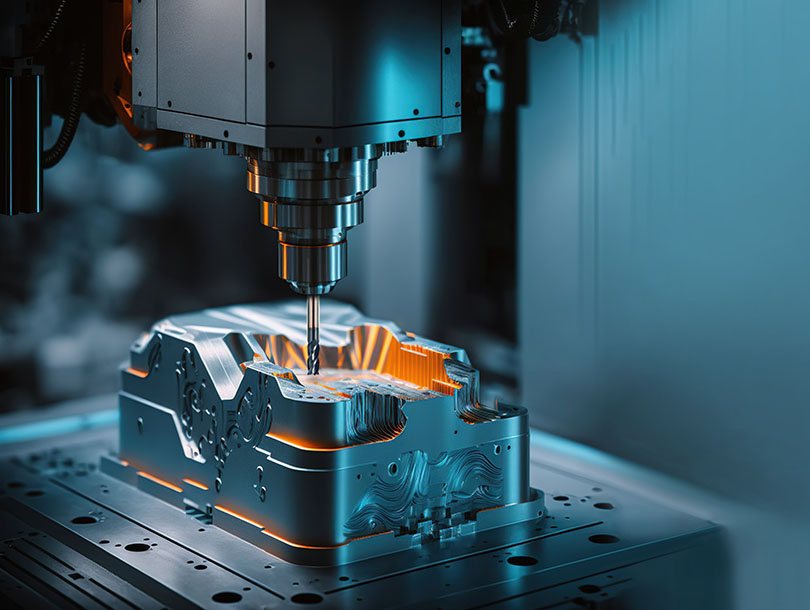
In the intricate realm of bolts and machining, the pursuit for accuracy and rate is a perpetual difficulty that requires meticulous focus to detail and tactical planning. When it comes to fasteners and machining applications, the product selection plays an essential role in determining the overall stamina, durability, deterioration resistance, and compatibility with the designated atmosphere. Accuracy machining includes various advanced approaches that make certain the limited tolerances and specifications required for bolts.In enhancement to CNC machining, other accuracy strategies like grinding, turning, milling, and drilling play vital duties in bolt production.To maximize bolt manufacturing processes, it is important to streamline procedures and execute efficient approaches that match precision machining strategies.
Report this page